Sponsored by CHR Hansen
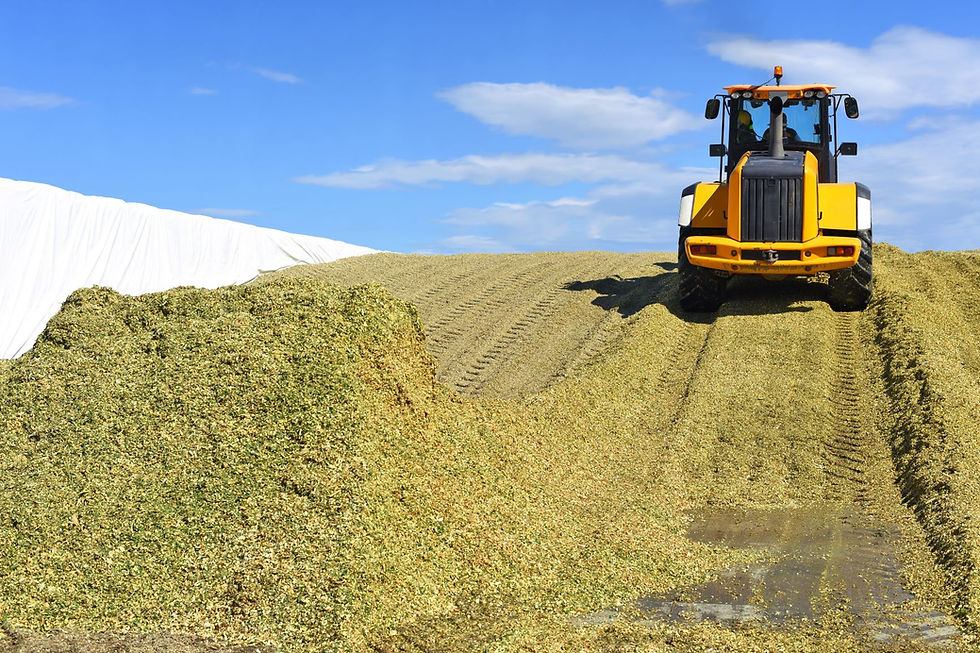
As you look at your corn silage crop standing in the field, the visual that you see is the result of the seed genetics, soil type, agronomy program, and the influence of mother nature. However, what comes next – harvest, fermentation, and storage--will be largely influenced by the people and processes you employ to get it through these stages. The final product (fermented corn silage) will represent a large portion of the cost and effectiveness of your entire feeding program. For example, effective fiber, starch digestibility, dry matter recovery, spoilage organisms, anti-nutritional factors (such as mycotoxins, and pathogenic bacteria), and aerobic stability are all influenced by how well the harvest and fermentation of the crop is managed by people; of course, mother nature will always be a factor.
Maturity (½ to ¾ milk line): As the corn plant progresses through life stages from a seedling to culmination of grain (seed) production at black layer, there is a trade-off between yield and digestibility. Harvesting at the proper maturity is the concept of cutting the corn crop when the balance between optimum yield and optimum digestibility is achieved. If you wait until black layer, you will achieve the maximum yield, but the starch and fiber digestibility may limit animal performance. At the same time, if you harvest too early, you may increase digestibility, but the reduced yield may result in a higher cost of production due to reduced yield per acre. For best results, harvest between ½ and ¾ milk line to have a good balance between digestibility and yield.
Dry Matter (32-36%): When ensiling corn silage, the dry matter content is important for several reasons. Corn that is wetter than ideal is easier to pack, but it may cause a loss in nutrients and dry matter due to effluent or runoff that takes valuable nutrients with it. On the other hand, silage that is too dry is difficult to pack and may result in a porous, aerobic silage mass that doesn’t ferment properly. At Chr. Hansen, we recommend an ideal range of 32-36% dry matter for best results.
Kernel Processing Score (KPS >70): Braman and Kurtz (2015) showed that the KPS of corn silage had a direct correlation to the amount of fecal starch. From this research, they concluded that adequate kernel processing reduced the variation in total tract starch digestibility. Under some circumstances, I have seen that adequate kernel processing can help produce as much as 4 pounds of additional milk per cow daily versus unprocessed. While our industry has made significant improvements, there are still many dairy farms that could benefit by improving KPS. Check your KPS during harvest and aim for a minimum of 70.
Inoculation (SILOSOLVE® FC): Science-based and research-proven. Using SILOSOLVE® FC inoculant will help provide a fast start and strong finish to the fermentation process, inhibit the growth of spoilage organisms, allow for early opening, and improve aerobic stability. While some would argue that mother nature can provide the bacteria for silage fermentation, I think we all know that mother nature is not always reliable, nor predictable. By inoculating with SILOSOLVE FC®, you have the best chance to get the highest quality with the least amount of nutrient losses.
Packing (meet or exceed the rule of 800): Proper silage fermentation is more likely to occur in the absence of oxygen. The goal of packing is to eliminate as much oxygen as possible via mechanical means. Following are some management ideas about how to do a better job of packing:
· Make sure the collective weight of your packing tractors = 800 * tons of forage delivered per hour. Thin layers (~4”) spread and packed in a progressive wedge configuration will facilitate achievement of higher density bunkers and piles.
· For bunker silos, alternate dumping, push-up and packing from left side-to-right side and vice-versa for uniform layer thickness, optimal packing time, and overall efficiency. The ideal packing tractor speed is 1.5-2.5 mph.
· Do not turn around on the pile.
· Make sure one set of wheels comes off the pile when changing direction in order to minimize loss of traction.
· Packing is complete when every square foot of top layer has tire tracks; having been run-over twice, and is smooth!
Another benefit to improved packing is to reduce the cost per ton of your silage storage. Increasing packing density from 16 to 18 lbs. DM/cu. ft. increases storage capacity by 12.5%. If you routinely store 6,000 tons of DM in a particular space, you could now store 6,750.
Sealing (keep the oxygen out until it’s time to feed it.) Once packing is completed, Chr. Hansen SILOSOLVE® OS is an option to spray on the top-layer before covering with plastic. SILOSOLVE® OS contains an oxygen scavenger that will help maintain an anaerobic environment under the plastic. I also recommend at least 2 layers of plastic: an oxygen barrier film plus a more durable plastic cover all capped off with tires / sidewalls, etc. Cover it quickly and make sure the tires are touching to avoid any loose areas for oxygen to penetrate the forage mass.
Safety: Practice good safety protocols. Harvest requires a lot of fixed assets and heavy equipment to achieve the end goal of quality feed. However, don’t lose sight of the fact that your human capital is the most important to your business. Please make sure that a good safety plan is in place in order to protect your workers and your farm from any accidents.
Pre-harvest planning meeting: If you have read this far and are not sure you have a handle on how to address each of the critical control points mentioned above, then I suggest you contact your Chr. Hansen representative and ask them to assist you in conducting a pre-harvest planning meeting. When holding your pre-harvest planning meeting, you can include the operator of the chopper, haulers, pushers, packers, nutritionist, forage specialist, etc. When conducted properly, the pre-harvest planning meeting can help you review harvest guidelines (maturity and moisture), set expectations (such as chop length, KPS, tons per hour, inoculant application, etc.), assign various tasks, and assess equipment needs such as the size and number of pack tractors. Additionally, when your workers are given a chance to contribute, they might have some ideas on how to improve safety and efficiency!

Comments